With all the recent shakeups in international trade - mostly the U.S. and China wrestling for control while everyone else tries to get a hold of what's even going on - I figured it would be a good time to share a story about the time I tried to get a product made in Europe.
Just over three years ago, while working on my first keyboard project, I got stuck. At the time, there was only a single choice for low profile mechanical key switches. And sadly, there were no aftermarket keycaps available for it at all. If you wanted to incorporate it in your design, you had to manufacture your own. And that's exactly what I set out to do.
Meet the MLDS keycap
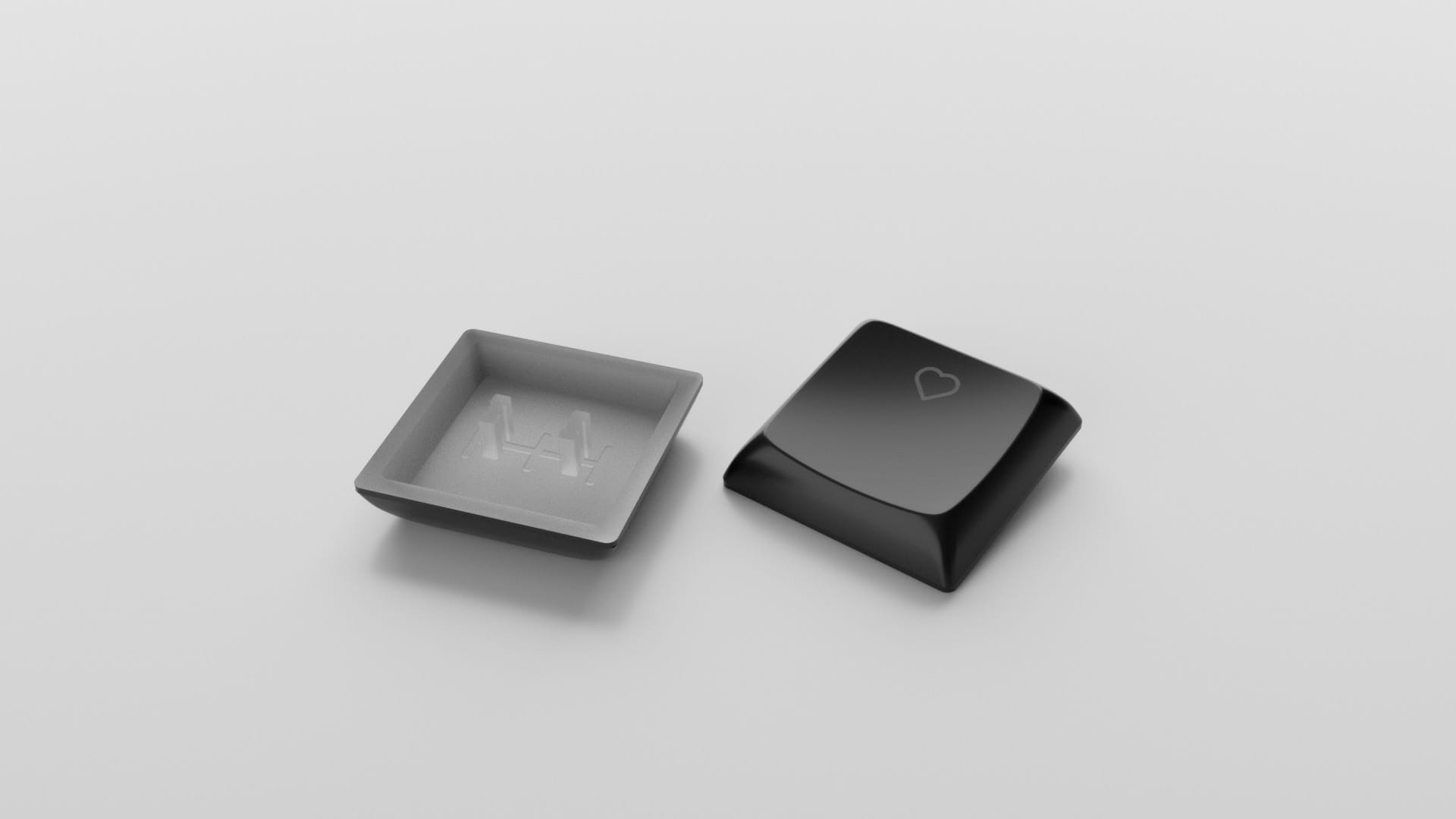
In case you're curious, that's muri (brand), large dish, spherical. They were designed with Kailh CPG1350 switches in mind, offering a spherical surface that would give you a noticeable feeling of depth while still keeping a low profile. They never made it to market, but if you're curious, the models are still available on GitHub.
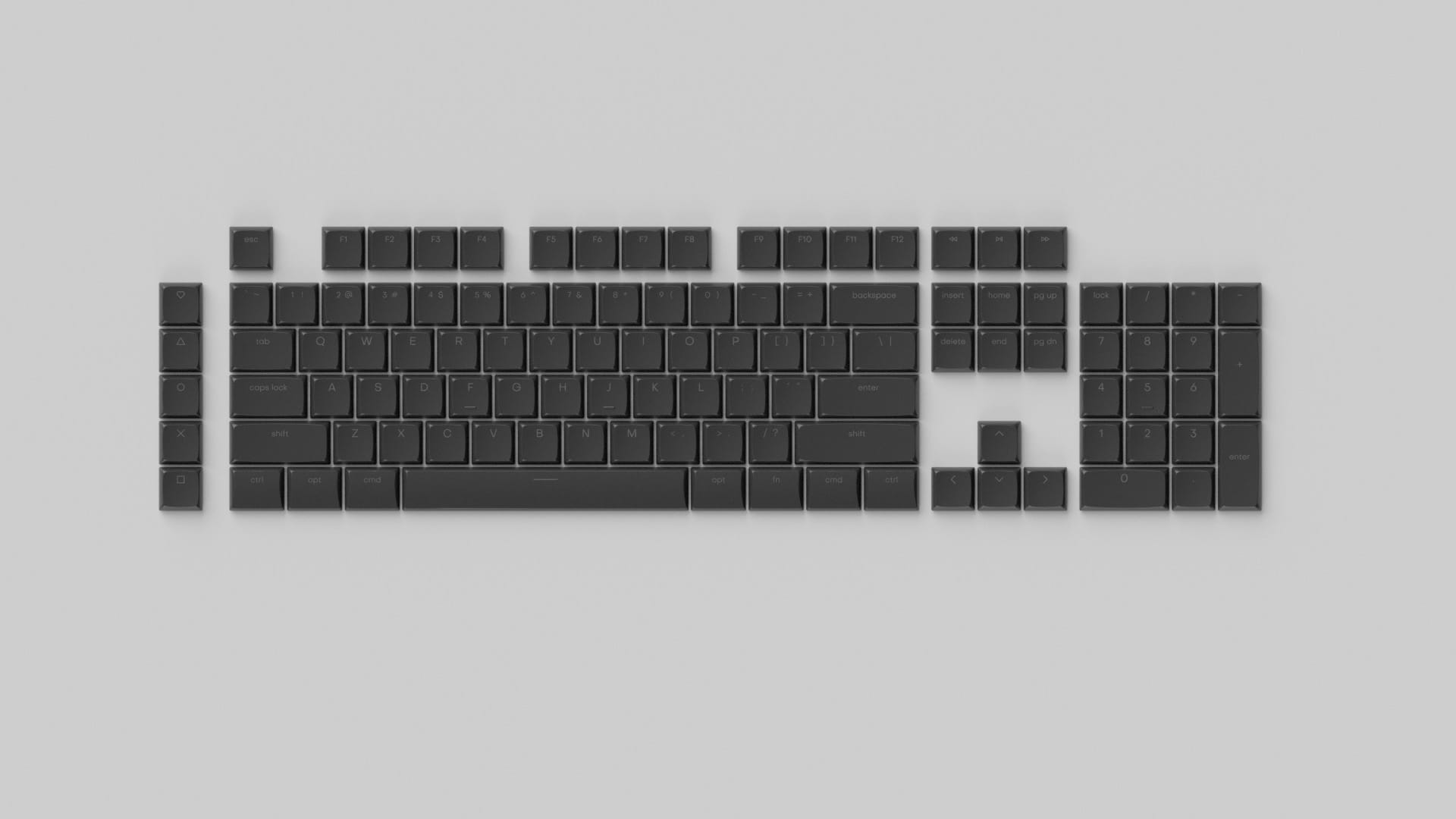
Following a few months of experimenting, 3d-printing prototypes and designing legends, it was time to get them made.
The manufacturing process
Injection molding is pretty much the only choice when it comes to manufacturing keycaps. It's the only method that allows for efficiently forming such fine features while maintaining enough structural integrity and a consistent surface finish. It's also very expensive.
The biggest cost factor is tooling. While the parts cost cents to manufacture, the molds needed to create these parts can easily run into tens or even hundreds of thousands of dollars. It's why you usually only jump for injection molding if you're planning on manufacturing at least tens of thousands of parts, ideally millions, to make up for that initial cost.
Importantly, making the physical object is just a part of the process. The keycaps would then still need to have their top surface coated in paint and the legends etched out. That's where the dealbreaker was.
Where it all fell apart
After speaking with several factories in Europe and in China, to my surprise, it was a small Lithuanian business that actually came up with by far the best offer. Four to five times below the next best one. That's a huge difference!
I for one, was really excited at the thought working with a European company. "Made in Europe" still carries some weight, and I didn't mind not having to deal with customs and overly long shipping times. So where did it all go wrong?
While I have no doubt in their ability to make top quality injection molded parts, unfortunately that's also the only thing they do. No post processing. No coatings, no etching. They assured me early on they would be able to provide a complete solution including coating and laser etching, but as we worked through it, it became clear that was not the case. Ultimately, that turned the project into a non-starter.
Innovation vs. integration
After doing more research, I am convinced that for any single part, you can probably find a company in Europe that'll do it cheaper and faster than in China. Where it gets problematic fast, is if your product complexity starts to grow - different parts, different materials, need for assembly, packaging etc. It really doesn't take a lot. Unless you're already at a scale where you can invest in building your own supply chain, it just make sense to pay extra and have someone else take care of all these problems.
And that's where I believe Chinese factories really shine. Convenience. Accomplishing the same thing in Europe that a single vendor would handle in China often requires going through two or more companies and all logistical overhead that comes with that.
This is not to say "Made in Europe" can't work. In fact, if anything I take this as a sign of the opportunities that lie ahead for anyone that can deliver on both fronts. The factories that already exist are often niche but exceptionally good at their craft. And let's not forget, sometimes time is the biggest issue, and you just can't afford to wait another 2 or 3 months before a prototype gets delivered.
All I'm really saying is, it's nowhere near as simple as one being straight up cheaper than the other. And by extension, just slapping on some tariffs here or there doesn't solve these issues.
Back to the keycaps
Going back to my little project, unfortunately I had to abandon the idea and published the models online for free use.
If a solution doesn't fully address the needs, it doesn't matter how cheap it is. The Chinese factory quoted me roughly $50,000 upfront for the complete process. That might be pocket change for an established company, but as a hobby project with about 2,000 sets spoken for and no other source of income to justify the investment, it just wasn't a risk I was willing to take at the time.
Do you have any manufacturing stories to share? Have you run into similar problems? I'm also convinced there's people out there that did make it work for themselves locally, and I'm all ears to hear some success stories too!